Sound deadening engine room – Pygmalion W32 #567 More images here.
After a long motor upwind and against the current, I began to research ways to reduce the engine and propeller sound that propogates into the cabin and cockpit.
Looking at the engine room and lazarette area – there are 3 echo chambers (lazarette and forward of each fuel tank) and 2 drums (two SS fuel tanks) as well as multiple fiberglass surfaces of the engine pan and hull to reflect the noise around the engine compartment and into the cockpit and cabin.
As designed and installed only the fiberglass deck with cockpit and removable cockpit sole and the engine compartment bulkhead is in place to stop the engine/transmission/exhaust and propeller noise from leaving the engine compartment.
Closer examination of the engine compartment bulkhead revealed multiple penetrations for engine room access, electrical, instruments, and plumbing. In addition, on the port and starboard there are the hollow areas between the deck and hull high on each side of the boat that allow sound to travel forward through this opening.
Underway, I noticed that when the lazarette hatch was opened the engine noise was equal to the noise in the engine compartment. By design, the lazarette bulkhead is open between the engine room and lazarette and the hatch is designed to allow air into the engine room.
Pygmalion was earlier modified to allow air into the engine from with a ~ 2” hole in the port cockpit bulworks and there is a 12 V fan exhaust the air from the engine room and into the cockpit.
So what I have is a noise generating engine (Beta 1505 – much quieter then the Volvo MB2B) in the engine compartment with multiple holes/openings with echo chambers and reflecting surfaces and NOTHING to absorb and/or block the sound energy from the cabin or cockpit.
Solutions needed:
- Block air/sound movement between compartments forward and aft.
- Absorb sound on as many surfaces in the engine room as possible.
- Product/s need to be easy to apply to the many angles and objects in the engine compartment.
- Inexpensive
- CG engine room approved materials
Materials (there are other similar products available):
Silent Running 1000 – a paintable material that is CG approved for engine room use.
- SR 1000 is recoatable in 1-2 hours and cures in 4 days to a flexible ~ 1mm thick material.
- After curing, I was able to bend a piece 90 deg w/o cracking.
- Easy to apply and very sticky, leaves a wavy surface that can be painted
- Applied in three coats by brush and close nap roller
- An air power spray gun is offered but not purchased
- Needs to be at least 1mm thick.
- $70 per gallon – 3 gallons used – 4 gallons would allow thicker coverage
- Water based for easy cleanup
- Low VOC

Sound foam “leaded” as sound absorbent liner.
- Possibly “Sound Down” there are other varieties.
- ½ thick and 1” thickness
- Expensive when new – I found used for pennies on the dollar by chance.
- 1/2” Birch furniture grade plywood – for sealing up lazarette bulkhead
- Cut to size then sealed and painted before installation.
- Aluminum foil self-adhesive duct insulation for wrapping SS fuel tanks.
- Pillows of shipping foam
- Scrap from where I work – seems this foam is flexible and I just jammed it in place up in the openings between the deck and hull.

Installation:
The best time to install the sound dampening materials is when the engine compartment is empty! I.e. during a repower. This would allow easier access to the hull and bulkhead for painting etc.
Since, I’m long past the repower project the installation was very difficult due to limited access to major openings from engine compartment to cabin.
Lazarette:
Sealing up the lazarette from the engine room was by far the most difficult task. I could just squeeze head first into the lazarette to reach the port and stbd openings to jam in pillows of foam in the bulwarks and install the ½” birch plywood over the large opening between the engine room and the lazarette.
I then applied spray foam to the exposed cracks and applied SR1000 in the lazarette, the underside of the lazarette and the underside of the hatch. Be sure to open the lazarette drain holes port and stbd so water drains into the engine bulge.
I also used some household door sealing strip on the deck to seal the lazarette hatch when closed.
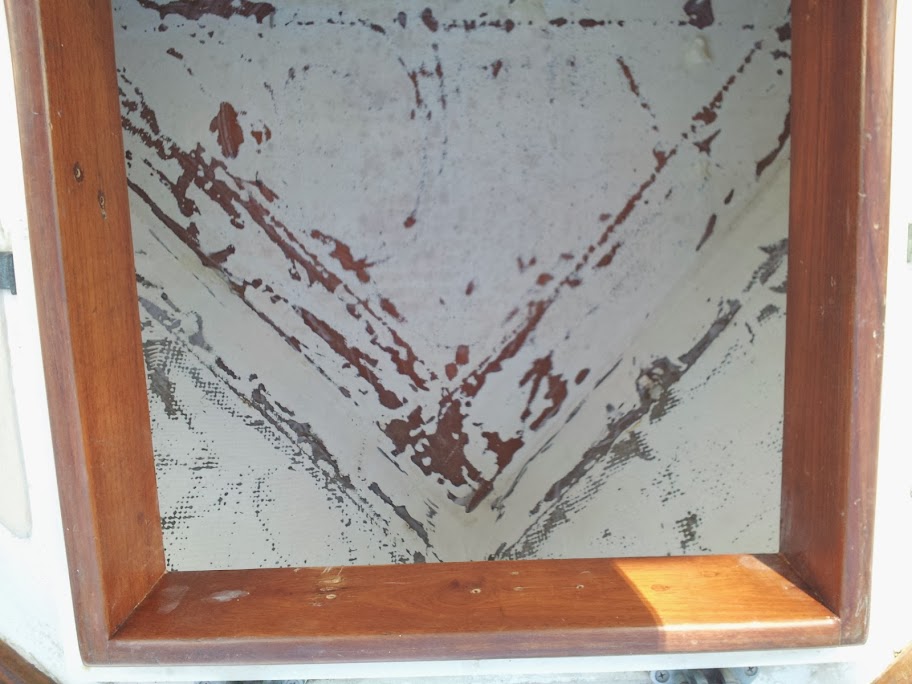
Figure 1 Lazarette prepped for SR 1000

Figure 2 STBD side lazarette sealed, foamed and SR1000 applied.

Figure 3 Lazarette finished
Sound foam installation:
I used heavy duty spray adhesive to secure the foam to the engine room boards and the bottom of the cockpit sole. The round washers are ¼” plywood sealed and painted with a screw in the center to hold the foam in place.

Figure 4 Underside of cockpit sole
Engine room boards were hinged where possible and backed with the sound foam.

Figure 5 Engine room boards - sound foam overlaps at the joint and on the lower edge.

Figure 6 View of 2nd step and upper board

Figure 7 View from the engine compartment with boards in place.
Silent Running 1000 installation:
The upper part of the engine room pan, the accessible interior of the hull and under the Lazarette was given 3 coats of SR1000. The first coat was a thin cover coat for the 2 thicker coats that together got the min thickness of 1mm. It was very hard to know the exact thickness even with the supplied gauge.
Several years ago, I had applied Interlux Bilgekote white to the engine room. Surface prep started out as sanding with power sanders but ended up with just using a liquid sand product that with a simple wipe on and dry which etched the surface of the paint. SR 1000 is a very sticky paint and it sticks very well to all the surfaces. (I recommend keeping it out of your hair)

Figure 8 Two sound sources with SR1000 later painted red to match engine.
After allowing the Silent Running four days of curing, I painted the engine room with Interlux bilgkote white and gray.
Fuel Tanks:
I covered the inside surface with aluminum faced self adhesive duct insulation to reduce the reflected sound off the SS tank walls. I could not reach the back side nor top well enough to completely wrap the fuel tanks.

Figure 11 Finished engine compartment the grey covers with one coat – verses 2 for the white.
What didn’t work:
I never found a good solution to plugging the void up in deck and hull space. The area is out of reach making the installation of any material difficult.
What needs to be done:
I was unable to treat the forward, stb and port under sides of the cockpit do to access issues and lack of more sound foam. If I have more of the ½ used foam I’d glue it to the engine room side of the cockpit walls and engine room bulkhead that are within reach.
Results:
There is a noticeable reduction in engine room noise – based on a former Westsailors comments and my observations both in the cockpit and cabin.
I also used a Samsung Droid Charge with free app Sound Meter 1.5.4 to take reading before the modification and after the addition of the sound materials. Note that the device microphone is limited to 98 DB by design- meaning that you can’t get a 100 db reading and that the before and after DB readings could be much higher in each case – really was a poor method of measuring sound.
There was a pretty good DB drop of 5 – 8 db depending on location of the sensor. ( a 10 DB drop is ½ the sound pressure)
Location
|
Slip
|
Slip
|
Slip
|
Underway
|
Underway
|
Transmission gear
|
Neutral
|
Neutral
|
Neutral
|
in gear
|
in gear
|
Project status
|
Before
|
After
|
After
|
Before
|
After
|
Engine RPM
|
800
|
800
|
2000
|
2000
|
2000
|
Table in cabin - db
|
80
|
75
|
78
|
91
|
92
|
Top of Frig - db
|
84
|
79
|
84
|
96
|
94
|
Second from top step - db
|
84
|
81
|
88
|
98
|
97
|
Center cockpit - db
|
89
|
78
|
83
|
96
|
97
|
cockpit near throttle - db
|
88
|
80
|
85
|
96
|
98
|
Cockpit opposite Throttle - db
|
88
|
80
|
83
|
Na
|
Na
|
cockpit Sole - db
|
na
|
85
|
91
|
98
|
98
|
Top of Lazarette closed - db
|
83
|
80
|
84
|
97
|
98
|
What is the next step:
I’d like to try hanging sound curtains in the engine room. I would hang them in the engine room to absorb the sound while NOT blocking air movement over the engine. The curtain would be easily movable for maintenance and should absorb the energy but not sure if engine room qualified.
I would also cover the fuel tanks with the sound deadening foam.
If you have a sound reduction project - please add as a reply.
Jay